Wind turbine blades are usually made from composite materials such as glass fibre and carbon fibre reinforced plastic and lightweight cores. These are during their lifespan exposed to fierce weather conditions.
Furthermore, future wind turbines are becoming larger and are in increasing number sited offshore which make servicing more expensive and challenging. This calls for very reliable wind turbines with as few stops as possible.
Developing New Methods
The purpose of DCCSM is therefore to develop new experimental and modelling methods covering everything from micro scale defects to cracks that are several metres long with the purpose of improving our understanding of what make defects develop into major cracks which can cause wind turbine blades to fail.
The methods have potential for the development of more damage tolerant composite materials resulting in more reliable wind turbine blade structures as well as prediction of the evolution of damages and cracks.
Lighter and Stronger Blades
Armed with such knowledge, manufacturers will be able to design lighter and stronger wind turbine blades with built-in sensors that will detect damage developing in the blade. Such equipment and modelling methods can be used to predict the strength of a wind turbine blade which has suffered damage and predict its remaining operational life.
The research of the Centre will be organised in four Work Packages (WPs) each reflecting the four most important length scales:
WP1: Nano-/microscale
WP2: Laminate scale
WP3: Sub-structural scale
WP4: Structural (or product) scale
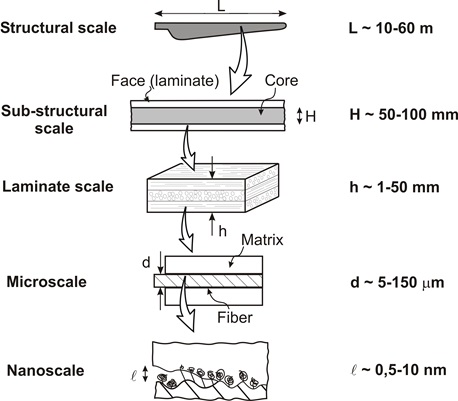
Schematic illustration of the multiscale approach to composite structures and materials for wind turbine blades. The entire wind turbine blade represents the structural scale, an example of a sub-structural part is a sandwich structure which has faces made of laminates that are made of composite materials consisting of fibres, matrix and the fibre/matrix interfaces.
A Strong Research Environment
The Centre is also a unifying entity for strengthening the research environment within composite structures and materials for wind turbines and will include for example the coordination and launch of future research projects. The project plans to train at least 20 PhD students and 3 postdocs and runs from 2010 to 2017.
Project partners:
DTU Wind Energy
Department of Mechanical Engineering at Aalborg University
DTU Civil Engineering
DTU Nanotech
DTU Mathematics
Siemens Wind Power
LM Wind Power
Fiberline Composites